Explore the transformative world of laser rust removal in our comprehensive guide. Discover the latest in technology, delve into safety considerations, and unlock the diverse applications of this cutting-edge method. Unveil the wonders that laser rust removal brings to industrial, automotive, and creative sectors.
Introduction
In the realm of metal restoration and maintenance, the advent of laser rust removal represents a significant leap forward in technology, promising a paradigm shift in how we address corrosion and rust-related challenges. This comprehensive guide aims to shed light on the intricacies of laser rust removal, exploring a myriad of aspects that encompass its working principles, effectiveness across various metals, safety considerations, advantages over traditional methods, applicability to diverse surfaces, the spectrum of lasers involved, environmental impact, process speed, potential impact on underlying surfaces, preventive maintenance applications, limitations, safety precautions, and suitability for painted or coated surfaces.
This exploration seeks to equip both seasoned professionals and curious enthusiasts with a profound understanding of laser rust removal, unraveling its potential and positioning it as a versatile and sustainable solution in the ever-evolving landscape of metal restoration and maintenance. As we embark on this journey through the nuances of laser technology, the guide aims to offer comprehensive insights that bridge the knowledge gap and empower individuals to make informed decisions in harnessing the capabilities of laser rust removal for enhanced efficiency and environmental consciousness.
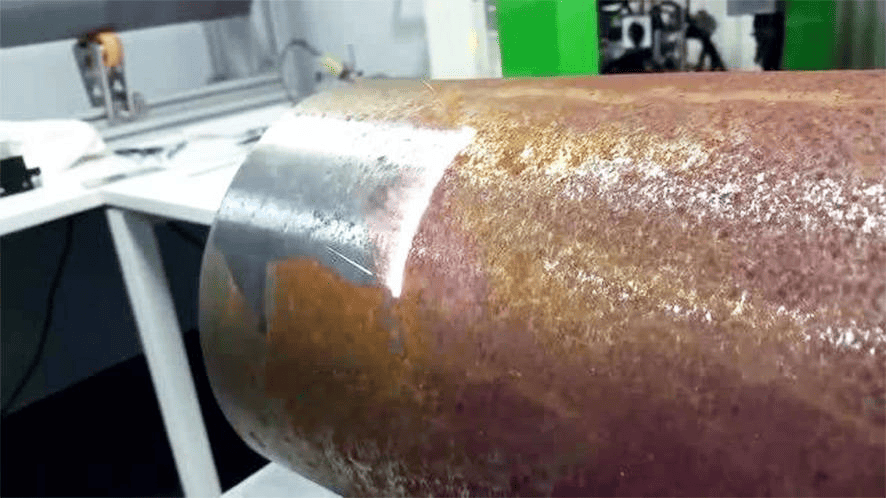
What is Laser Rust Removal?
Laser rust removal, a cutting-edge technology at the forefront of the machine industry, represents a revolutionary approach to eradicating rust and corrosion from metal surfaces. At its core, this process harnesses the power of high-intensity laser beams to achieve a meticulous and non-contact removal of rust, providing a stark departure from conventional methods. The precision and control offered by laser rust removal make it a highly appealing alternative, especially when compared to more traditional techniques. This advanced technology utilizes the focused energy of lasers to vaporize and ablate rust, leaving behind a clean and restored metal surface.
The efficiency of laser rust removal is particularly noteworthy, as it ensures a targeted removal without causing damage to the underlying material. This method not only surpasses the limitations of abrasive methods, such as sandblasting or chemical treatments, but it also minimizes waste generation, contributing to a more environmentally friendly approach to industrial cleaning. As we delve into the intricacies of laser rust removal, it becomes evident that its advantages extend beyond the immediate removal of rust, encompassing factors such as safety, precision, and environmental impact. This paradigm shift in rust removal technology holds great promise for industries relying on pristine metal surfaces, offering a glimpse into the future of efficient and sustainable industrial cleaning practices.
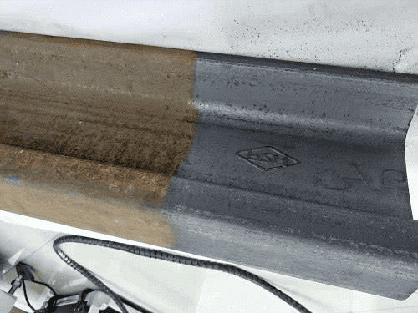
How Does Laser Rust Removal Work?
Laser rust removal operates on the principle of laser ablation, a process that harnesses high-energy laser beams to effectively eliminate rust or oxide layers from surfaces. This method ensures a clean and uncontaminated metal surface, free from the detrimental effects of rust or corrosion. The key components of laser rust removal include:
Laser Ablation:
Principle: The intense heat generated by the laser vaporizes the rust, essentially removing it layer by layer.
Effective Rust Elimination: The process of laser ablation ensures a thorough removal of rust, leaving behind a pristine metal surface.
Precision Control:
Adjustable Intensity: Laser systems provide precise control over the intensity of the laser beam, allowing for tailored rust removal without adversely affecting the underlying metal.
Focused Beam: The ability to focus the laser beam enhances precision, enabling targeted rust removal in specific areas without causing damage to adjacent surfaces.
Laser rust removal, through the mechanism of laser ablation and precision control, exemplifies a cutting-edge approach to maintaining and restoring metal surfaces, offering unparalleled advantages in terms of efficiency and effectiveness. The following sections will further explore the diverse applications, environmental considerations, safety protocols, and maintenance practices associated with laser cleaning machines, providing a holistic understanding of their role in the modern industrial landscape.
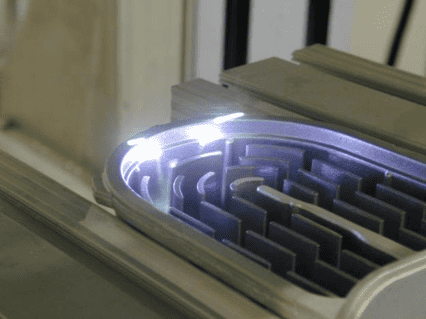
Is Laser Rust Removal Effective on All Types of Metals?
Laser rust removal is effective on a wide range of metals, including steel, iron, aluminum, and more. Its versatility stems from the ability to adjust laser parameters to suit the specific properties of different metals.
Versatility: Laser systems can be fine-tuned to handle the characteristics of various metals, making them adaptable to different applications.
Are There Safety Concerns Associated with Laser Rust Removal?
Laser rust removal is a highly effective method that can be applied to a wide array of metals, showcasing its versatility and adaptability. Key points include:
Metal Compatibility: Laser rust removal is effective on diverse metals, including steel, iron, aluminum, and more. The technology’s flexibility allows it to cater to the unique properties of different metals.
Versatility: Laser systems can be fine-tuned to handle the characteristics of various metals, making them adaptable to different applications. This versatility enhances the efficiency and precision of the cleaning process, making it suitable for a broad range of industrial needs.
What Are the Advantages of Using Laser Rust Removal Over Traditional Methods?
While laser rust removal is generally a safe and efficient method, it is crucial to observe proper safety measures to mitigate potential risks. Important considerations include:
Eye Protection: The intense laser beams used in the rust removal process pose a risk to the eyes. Laser safety glasses are essential to shield operators’ eyes and prevent potential damage.
Ventilation: Adequate ventilation is a critical safety measure to disperse any fumes generated during the laser cleaning process. This ensures a safe working environment and prevents the inhalation of harmful by-products.
Operator Training: Proper training is imperative for operators to handle laser cleaning equipment safely and effectively. This includes understanding the technology, implementing safety protocols, and troubleshooting potential issues. Training enhances the overall competence of operators, reducing the likelihood of accidents or errors.
Can Laser Rust Removal Be Used on Large or Intricate Surfaces?
Laser rust removal exhibits remarkable versatility, making it suitable for both large structural elements and intricate components. The scalability of laser systems is a pivotal feature, allowing them to adapt to different surface sizes and intricacies. This adaptability ensures that laser cleaning machines can effectively address a wide range of applications, from detailed machinery components to expansive surfaces.
Scalability: Laser systems can be adapted to handle different surface sizes, from small, detailed components to large structural elements. This scalability enhances the applicability of laser rust removal across diverse industrial contexts.
What Types of Lasers Are Commonly Used for Rust Removal?
Various types of lasers find application in rust removal processes, each offering unique advantages tailored to specific industrial needs.
Fiber Lasers: Renowned for their high power and efficiency, fiber lasers are commonly employed in industrial applications. Their ability to deliver intense laser beams makes them effective for removing rust from surfaces with varying levels of corrosion.
Nd:YAG Lasers: These lasers are known for their versatility and precision, making them suitable for intricate tasks such as rust removal. Nd:YAG lasers can be finely tuned to target specific areas, making them ideal for applications where precision is paramount.
CO2 Lasers: While not as common as fiber or Nd:YAG lasers, CO2 lasers offer specific advantages in certain rust removal processes. Their effectiveness in specific applications contributes to the diverse toolkit available for industrial cleaning.
Is Laser Rust Removal Environmentally Friendly?
Laser rust removal is considered environmentally friendly, aligning with sustainability goals and minimizing the ecological impact associated with traditional cleaning methods.
Reduced Waste: Laser rust removal generates minimal waste, contributing to sustainability goals by minimizing the environmental footprint of industrial cleaning processes. The focused nature of the laser ensures that only the rust or contaminants are removed, leaving the underlying material intact.
No Chemicals: One of the key environmentally friendly aspects of laser rust removal is its chemical-free nature. Unlike traditional methods that may involve harsh chemicals, laser cleaning eliminates the need for environmentally harmful substances, further reducing the ecological impact of industrial cleaning.
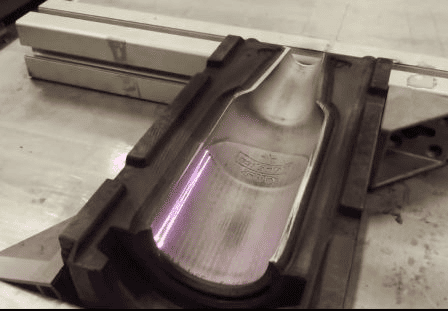
How Fast Is the Laser Rust Removal Process?
The speed of laser rust removal depends on factors such as laser power, surface area, and the thickness of the rust layer. Generally, the process is efficient, and its speed contributes to increased productivity.
Efficiency: Laser systems offer rapid rust removal, making them time-efficient for various applications. The speed of the laser rust removal process is influenced by factors such as laser power, surface area, and the thickness of the rust layer.
Factors Affecting Speed: Laser rust removal speed is influenced by laser power, the size of the surface to be cleaned, and the thickness of the rust layer. Higher laser power and smaller rust thickness contribute to faster cleaning.
Does Laser Rust Removal Damage the Underlying Metal Surface?
When performed by trained operators using appropriate parameters, laser rust removal minimizes the risk of damaging the underlying metal. The precise control over the process ensures that only rust is removed, leaving the metal intact.
Surface Preservation: Laser systems excel at preserving the integrity of the underlying metal surface. When operated by trained professionals with appropriate parameters, laser rust removal minimizes the risk of damaging the underlying metal, ensuring that only rust is removed.
Precision Control: The precise control over the laser cleaning process ensures that only the rust is targeted, leaving the metal surface intact.
Can Laser Rust Removal Be Used for Preventive Maintenance?
Laser rust removal can be employed for preventive maintenance by removing early signs of corrosion before they escalate. Regular treatment can extend the lifespan of metal components and structures.
Preserving Structural Integrity: Laser rust removal can be employed for preventive maintenance by removing early signs of corrosion before they escalate. Regular treatment can extend the lifespan of metal components and structures, preserving their structural integrity.
Early Intervention: Addressing rust in its early stages helps maintain the structural integrity of metal assets, preventing costly damage.
What Safety Precautions Should Be Taken During Laser Rust Removal?
Adhering to safety precautions is crucial for the well-being of operators and the success of the process:
Eye Protection: Laser safety glasses are mandatory to protect against direct or scattered laser beams, ensuring the safety of operators’ eyes.
Ventilation: Proper ventilation is crucial to disperse fumes and prevent the buildup of potentially harmful byproducts, maintaining a safe working environment.
Operator Training: Thorough training of operators is essential to handle the equipment safely and efficiently, minimizing the risk of accidents and ensuring the success of the laser rust removal process.
Can Laser Rust Removal Be Used on Painted or Coated Surfaces?
Laser rust removal represents a groundbreaking advancement in surface treatment, offering a unique solution for dealing with rust on painted or coated surfaces. Here are key points to consider:
Selective Treatment: One of the most remarkable features of laser rust removal is its ability to provide selective treatment. Laser systems are designed to target rusted areas with pinpoint accuracy while preserving the integrity of painted or coated surfaces. This precision ensures that the removal process is focused solely on the rusted regions, leaving the surrounding paint or coating unharmed.
Preservation of Coatings: Traditional methods of rust removal, such as abrasive techniques or chemical processes, often pose a risk to the underlying coatings on surfaces. Laser cleaning mitigates this risk by selectively eliminating rust without causing damage to the protective coatings. This capability is particularly advantageous in industries where preserving the aesthetic or functional aspects of painted or coated surfaces is crucial.
Minimized Surface Damage: Laser rust removal minimizes surface damage by avoiding the need for abrasive materials or harsh chemicals. The non-contact nature of laser cleaning reduces the risk of scratches, abrasions, or chemical reactions that can compromise the structural integrity of painted or coated surfaces.
Versatility in Applications: The applicability of laser rust removal extends across various industries, including automotive, aerospace, maritime, and infrastructure. Its ability to work on painted or coated surfaces makes it a versatile solution for addressing rust-related challenges in diverse settings.
Efficiency and Precision: Laser systems operate with high precision, ensuring that rust is removed efficiently without compromising the quality of the underlying surfaces. This efficiency not only streamlines the cleaning process but also contributes to cost-effectiveness by minimizing the need for additional touch-ups or re-coating.
What Industries or Applications Benefit Most from Laser Rust Removal?
Laser rust removal has emerged as a game-changing technology with diverse applications across multiple industries, proving to be a highly effective and efficient method for addressing rust-related challenges.
Automotive Industry:
Laser rust removal is particularly advantageous in the automotive sector, where it excels at removing rust from various vehicle components. From the surface of car bodies to intricate parts like exhaust systems or chassis components, laser cleaning ensures a thorough and precise rust removal process. This not only enhances the aesthetic appeal of the vehicles but also contributes to the longevity and performance of automotive parts.
Marine Industry:
In the marine sector, where exposure to harsh and corrosive environments is inevitable, laser rust removal proves to be a reliable solution for treating rust on ship structures. Ships and offshore structures are often susceptible to corrosion due to constant exposure to saltwater, and laser cleaning offers a non-intrusive method for maintaining the integrity of metal surfaces without causing damage to the underlying structures.
Aerospace Sector:
The aerospace industry benefits significantly from laser rust removal, employing this advanced technique for precision cleaning of rust on critical aircraft parts. Given the strict quality and safety standards in aerospace manufacturing, laser cleaning ensures that rust is meticulously removed from components without compromising their structural integrity. This is crucial for maintaining the safety and reliability of aircraft, where even small rust particles can have significant consequences.
Heritage Conservation:
Laser rust removal plays a vital role in heritage conservation by offering a non-abrasive and precise method for restoring historical metal artifacts. This is particularly valuable when dealing with delicate or intricate pieces where traditional methods may be too harsh and risk causing damage. The ability to selectively remove rust while preserving the original surface of historical artifacts is a key benefit in the field of heritage preservation.
As industries continue to recognize the versatility and effectiveness of laser rust removal, its applications are likely to expand further, contributing to enhanced efficiency, cost-effectiveness, and environmental sustainability across various sectors.
Conclusion
In conclusion, laser rust removal has emerged as a cutting-edge technology, leading the way in the realm of metal surface restoration with its remarkable combination of precision, efficiency, and environmental consciousness. Throughout this guide, we’ve delved into the intricacies of laser cleaning machines, providing a detailed exploration of their working principles, diverse applications, environmental impact, safety measures, and maintenance requirements.
As industries undergo constant transformation, it is imperative to recognize the pivotal role played by laser rust removal in the preservation and enhancement of metal assets. The advantages it offers over traditional methods, such as abrasive blasting or chemical cleaning, are substantial. Laser cleaning not only ensures a meticulous removal of contaminants but also does so without generating harmful by-products, making it an eco-friendly solution.
The precision of laser technology minimizes damage to the substrate, extending the lifespan of materials and reducing the need for frequent replacements. Moreover, its versatility allows for applications across various industries, from automotive and aerospace to historical artifact restoration. As we navigate the dynamic landscape of industrial advancements, laser rust removal stands as a transformative force, reflecting a commitment to technological innovation that aligns with both efficiency and sustainability. This guide, whether for seasoned professionals or curious enthusiasts, aims to foster a profound understanding of the capabilities and advantages that laser cleaning machines bring to the forefront of industrial cleaning processes.