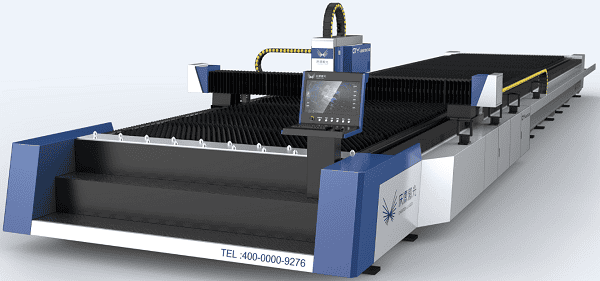
Have you ever thought of the applications of laser cutting in elevator equipment manufacturing? Have you thought of the success that they’ve brought to the entirety of the industry?
Studies have shown that elevator businesses enjoy huge profit margins and healthy revenues. So, if you are in this business and you haven’t even considered laser cutting machines, you’re left behind.
Our guide will focus on the various applications of laser cutting for the elevator industry. We’ll talk about why it’s used there, how they’re used, and other crucial information about them.
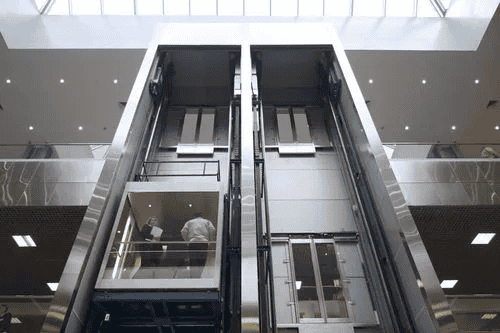
Contents
The Essence of Laser Cutting: Speed and Accuracy
Prior to us connecting the idea of laser cutting with elevator equipment, we first need to understand its essence and working principle. In the simplest terms, laser cutting is an advanced technique that uses high-beam lasers to precisely and accurately cut materials and workpieces.
In a more scientific approach, the laser will be focused on a spot in the workpiece. That will then generate heat, which will be enough to vaporize or melt the material.
Understanding the Elevator Industry
The elevator industry follows a long line of history. From a device used to carry goods in the 1850s, to what we know of it today now, it’s evident that the development and progress are continuous, and scarily rapid.
Besides the things we see when we get on the elevator, there are important components that make it up:
Car/Cabin
The primary part of the elevator, what we see. This is what transports people and goods.
Machine
Standard machines typically consist of motors, brakes, bed plates, and sheaves. It is what makes the elevator function like how it should.
Cable
It is what’s responsible for the passing over of the sheave to the counterweight. In simpler terms, it’s the component responsible of pulling and pushing the cabin or car up or down.
Control Cabinet
Otherwise known as the controller, it’s the brain or like the “CPU” of the elevator. It’s where all the magic happens when an elevator is operated.
NOTE: Can be automatic or manual, depending on the model and make of the machine.
Landing Doors
These are pretty self-explanatory; they are the doors that allow you to enter and exit the elevator cabin/car.
Counterweight
The component that balances the elevator. It needs to be the same amount as the car in order to control and pull itself.
These are among the most important and most-common elevator parts. Furthermore, they are also the components that are often made of metal and cut using various techniques.
It’s important to know and understand them as they are the ones you will be handling.
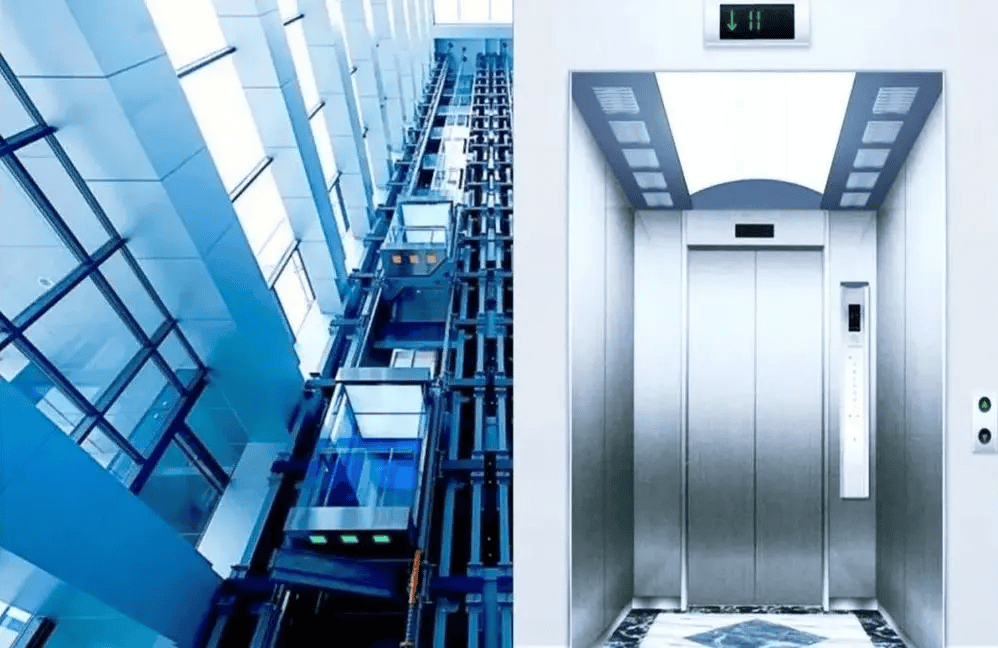
Applications of Laser Cutting in Elevator Equipment Manufacturing: The Pros and Advantages
Laser cutting machines are arguably expensive, but to what extend would you accept its cost considering its advantages?
High Flexibility in Processing
The first advantage of laser cutting in elevator equipment would be flexibility and versatility. Traditional technologies are known to have difficulty in handling small, detailed, and intricate shapes as patterns; these are slowly become varied and complicated.
Thanks to laser cutting’s great automation, technological capability, and intelligence, they’re able to handle complexly shaped workpieces with ease, saving labor costs and streamlining production procedures.
NOTE: Since they’re programmed and pre-written, the movement and patterns of laser cutters will almost always be the same. There’s a 99.98% chance of the patterns and repetitions to be exactly the same.
Brief Cycle of Processing
The elevator business contains tons of unique models of sheet metal components; components that often need to be modified and altered fast. Mold production can restrict this labor-intensive and complicated metalworking procedure of traditional means
However, you can eliminate these constraints through the use of flexible laser cutting technology. Laser cutting technology can also lower the development costs, as well as simplify programming.
Effective Cutting
Last but most definitely not least would be the creation of elevator elements. If there’s anything in particular, they’ll be the decorative stainless-steel plates, the interior of the elevator, the gear, and drive, which all require frequent high-quality surface polish.
While conventional punching and cutting is known to cause surface damage, the process of laser cutting duly removes mechanical stress. This helps stop deformation and further warping of the material.
Furthermore, it also ups product grade, enhances product quality, and increases the competitiveness of the business.
Laser Cutting vs. Waterjet Cutting Elevator Equipment
When manufacturing elevator equipment, selecting between laser and waterjet cutting depends on a few factors. These factors will dictate whether your products are winners or losers.
Here are some of the key factors to consider before you make the decision:
Material Thickness
Laser cutting excels in precision for metals up to 0.375” thick. Waterjet cutting handles thicker materials but with less accuracy.
Heat Impact
When it comes to heat, water is the best. Waterjet cutting is heat-free, preventing the metals to warp while being operated. However, it can deform thin materials under high pressure. Laser cutting generates heat, which can affect thin metals and intricate patterns.
If done in the most optimal ways possible, laser cutting might just be the perfect fit.
Precision
Laser cutting offers tighter tolerances (about 0.002”) compared to waterjet cutting (0.008”). This simply means that lasers are more precise and accurate than waterjets in the case of heavy-duty metals.
Speed
Last, and most definitely not least is speed. Generally speaking, lasers are faster and more urgent. They’re able to cut 20-1000” per minute, while waterjets cut 1-20” per minute. It’s a big difference considering price, availability, and overall quality of the work.
For precise and fast cutting of elevator parts, laser cutting is often the best choice. However, for thicker materials, waterjet cutting may be more suitable.
Get World-Class-Quality Laser Cutters From Cheeron Laser
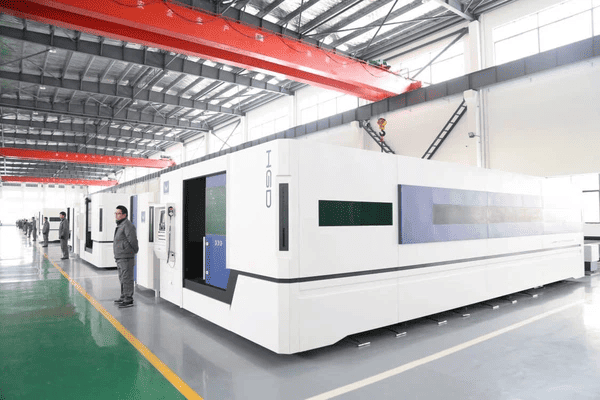
Do bad cuts, inconsistent production, and unsafe features haunt you? Don’t worry, we here at Cheeron Laser will take you away from that! Being in the industry for more than a decade, we take pride in our constant development and improvement in our craft.
In the elevator industry, consistency and accuracy are two of the most important things. Not having one can be a disaster. So, our team of experts and developmental virtuosos here at Cheeron Laser won’t leave you hanging! We’ll get you whatever you need in the best ways possible!
Whatever laser machine or service you need, we’ll be sure to help you out on it! Just reach out to us! We can also give you a free estimate or free quote, all you have to do is send us a message!