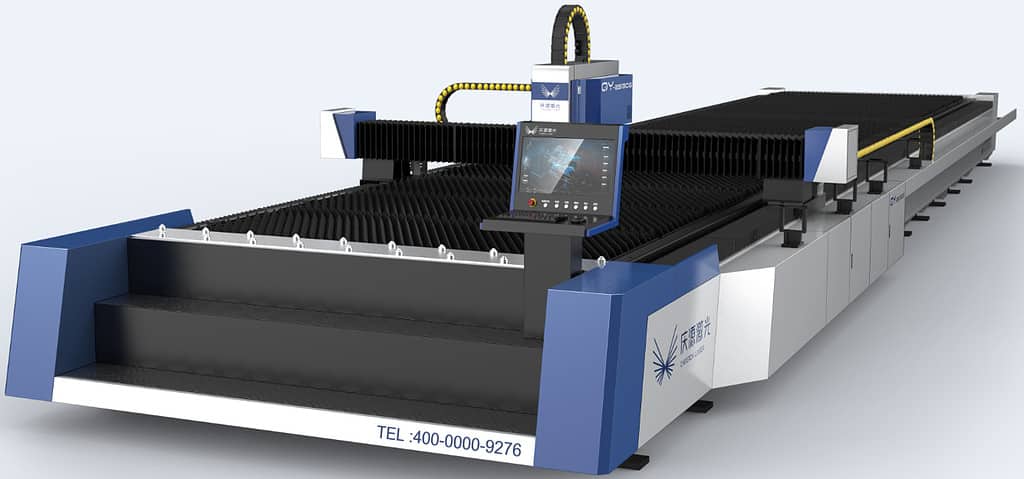
Before the popularization of laser applications, carbon steel medium and thick plates usually use traditional cutting processes such as plasma cutting, flame cutting, and high-pressure water jet cutting, among which plasma cutting is the representative. In recent years, with the application and development of the laser cutting industry, the disadvantages of plasma cutting are gradually reflected.
Plasma cutting is a processing method that uses the heat of a high-temperature plasma arc to locally melt the metal at the incision of the workpiece, and removes the molten metal with the help of the momentum of high-speed plasma to form an incision.
For plasma cutting, the cutting current of the plasma power supply is the most important cutting process parameter, which directly determines the cutting thickness and speed. The greater the current, the stronger the arc energy, and the cutting speed and thickness. At the same time, the increase of the cutting current also leads to the increase of the arc diameter, which also leads to the thickening of the arc and the wider the slit. Also due to the thickening of the workpiece, the cutting section of the plasma is rougher and the perpendicularity is worse, even due to the increase of the arc diameter. Makes the plasma unable to cut precision holes. And these problems can be easily solved for fiber laser cutting.
For traditional plasma cutting, the obvious advantages of fiber laser cutting are as follows:
The first is the cutting speed, which is a very important production index for processors, which is directly linked to production efficiency. Laser cutting is much faster than plasma in terms of perforation cutting speed, especially in the processing of medium and thin plates. Especially obvious.
The second is the cutting effect. Due to its characteristics, laser cutting can meet high roughness requirements on the cutting end face. Compared with plasma cutting, it has the obvious advantages of high precision, smooth end face and less slag. At the same time, the advantages are narrower slits, lower end face taper and higher verticality.
At the same time, laser cutting also has more advantages in production environment and cost consumables.
Fiber Laser Cutter VS Plasma Cutter
Cutting speed
Plasma: slower.
Laser cutting: especially for fast medium and thin sheets.
Cut quality
Plasma: poor accuracy, obvious slag hanging, rough end face, wide slit, large thermal influence and large taper.
Laser cutting: high precision, very little slag hanging, smooth section, narrow slit, small thermal influence, small taper.
Cutting environment
Plasma: dense smoke, harmful gas, loud noise.
Laser cutting: clean and tidy, fully enclosed, relatively low noise.
Cutting Consumables
Plasma: Electrodes, nozzles, protective cover The average service life of electrode nozzles is 3-4 hours.
Laser cutting: nozzle, protective lens, average 200 hours service life (high-power equipment consumables have a relatively short service life).