Explore the world of precision with our comprehensive guide. Uncover the secrets to maximizing efficiency and unleashing the full potential of laser cutting technology in aluminum materials. From intricate designs to optimal settings, this guide is your key to mastering the art of precision in aluminum laser cutting. Elevate your skills and achieve impeccable results with our expert insights and practical tips.
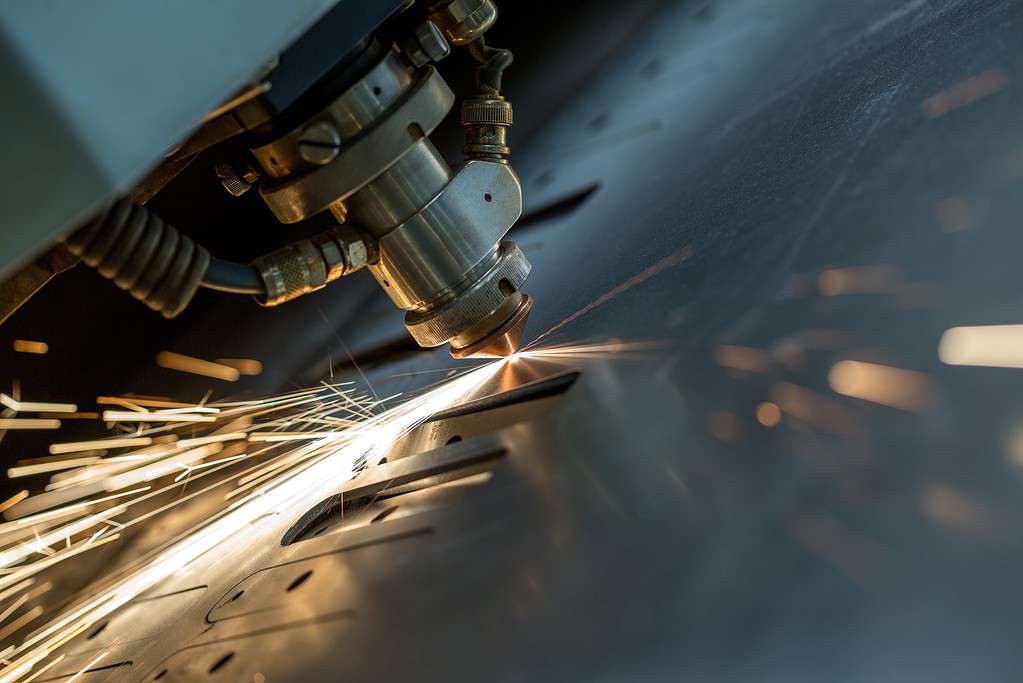
Introduction
In the realm of sheet metal cutting, laser cutting emerges as an unparalleled solution, epitomizing precision and efficiency. This in-depth guide delves into the specialized application of laser cutting, focusing specifically on its utilization in the context of aluminum—a lightweight and corrosion-resistant metal that finds extensive use in industries such as aerospace and electronics.
Serving as a valuable resource for both seasoned professionals in the field and curious enthusiasts alike, this guide takes readers on a journey from the fundamental principles of laser cutting to a comprehensive exploration of its advantages, inherent challenges, and essential safety measures. By the end of this exploration, readers will gain a profound understanding of how to harness the power of laser technology for cutting aluminum sheets, unlocking new possibilities in the ever-evolving landscape of sheet metal fabrication.
What is Laser Cutting for Aluminum?
Laser cutting for aluminum is a cutting-edge technique that employs a high-powered laser beam to intricately and precisely cut through aluminum sheets. This advanced method represents a non-contact approach, distinguishing itself by enabling the creation of intricate designs and the formation of complex shapes with minimal material waste. Industries that prioritize precision and efficiency in aluminum fabrication find laser cutting to be a go-to solution for their needs.
The technology’s ability to deliver precise and clean cuts contributes to its widespread adoption in various applications within the aluminum processing sector. This innovative approach to aluminum cutting has not only elevated the standards of precision in the industry but has also significantly reduced material waste, making it an environmentally conscious choice. As industries continue to seek methods that enhance both the quality and efficiency of their processes, laser cutting for aluminum has emerged as a transformative solution, playing a pivotal role in reshaping the landscape of aluminum fabrication.
What Are the Advantages of Using Laser Cutting for Aluminum Over Other Methods?
Laser cutting stands out as a superior method for processing aluminum in the machine industry, offering a range of advantages over alternative cutting methods:
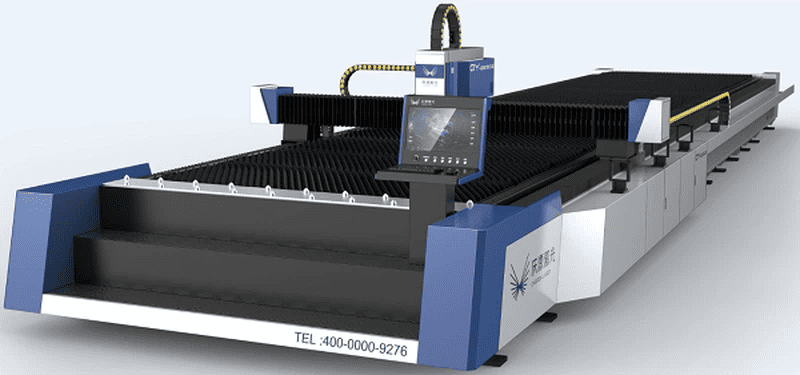
1. Precision:
Laser cutting excels in providing unparalleled precision, making it the preferred choice for intricate designs and detailed cuts. The focused laser beam ensures accuracy in shaping aluminum components, meeting tight tolerances and specifications.
2. Versatility:
Laser cutting exhibits remarkable versatility by accommodating various aluminum alloys and thicknesses. This flexibility allows manufacturers to work with a diverse range of materials, meeting specific project requirements without the need for constant adjustments or changes in cutting tools.
3. Minimal Material Waste:
One of the significant benefits of laser cutting for aluminum is the minimal material waste it produces. The precision of the laser beam enables efficient use of the material, reducing scrap and optimizing material usage. This not only contributes to cost savings but also aligns with sustainable manufacturing practices.
4. Non-Contact Cutting:
Laser cutting is a non-contact method, as the laser beam doesn’t physically touch the aluminum surface. This characteristic eliminates the risk of tool wear, reducing the need for frequent tool replacements and maintenance. Additionally, non-contact cutting minimizes the chance of contamination, ensuring the integrity of the aluminum material.
5. Speed and Efficiency:
Laser cutting is renowned for its speed and efficiency in the machining process. The high cutting speeds of lasers contribute to shorter production times, improving overall manufacturing efficiency. This quick turnaround is particularly beneficial in industries where time-sensitive production schedules are crucial.
In summary, the advantages of using laser cutting for aluminum in the machine industry are multifaceted. Its precision, versatility, minimal material waste, non-contact cutting, and speed make it a go-to method for achieving high-quality results while optimizing resource utilization and production timelines. As technology continues to advance, laser cutting remains at the forefront of aluminum processing, driving innovation and efficiency in the manufacturing sector.
Are There Any Limitations or Challenges When Laser Cutting Aluminum?
Laser cutting technology has revolutionized metal fabrication processes, offering immense versatility and precision. However, when it comes to laser cutting aluminum, there are certain limitations and challenges that manufacturers and fabricators need to be aware of:
Reflectivity: One of the primary challenges in laser cutting aluminum is its high reflectivity. Aluminum reflects laser beams more effectively than some other metals, such as steel. This can result in reduced laser absorption, making it challenging to achieve optimal cutting conditions. To overcome this, adjustments in cutting parameters, such as laser power and beam focus, are often necessary to enhance absorption and maintain cutting efficiency.
Material Thickness: While laser cutting is an effective method for various thicknesses of aluminum, extremely thick sheets may present challenges. The limitations are often associated with the power of the laser source. For thicker materials, alternative cutting methods like water jet cutting or plasma cutting might be more suitable. These methods can handle greater material thicknesses with ease, providing a viable alternative when laser cutting alone may not suffice.
Initial Setup Costs: Implementing laser cutting technology for aluminum fabrication involves significant initial setup costs. The machinery and equipment required, including high-powered lasers, precise optics, and control systems, can be expensive. However, it’s crucial to note that while the initial investment may seem high, the long-term benefits often outweigh these costs. Laser cutting offers enhanced precision, reduced waste, and increased efficiency, leading to improved productivity and cost-effectiveness over time.
How Precise is Laser Cutting When Working with Aluminum Materials?
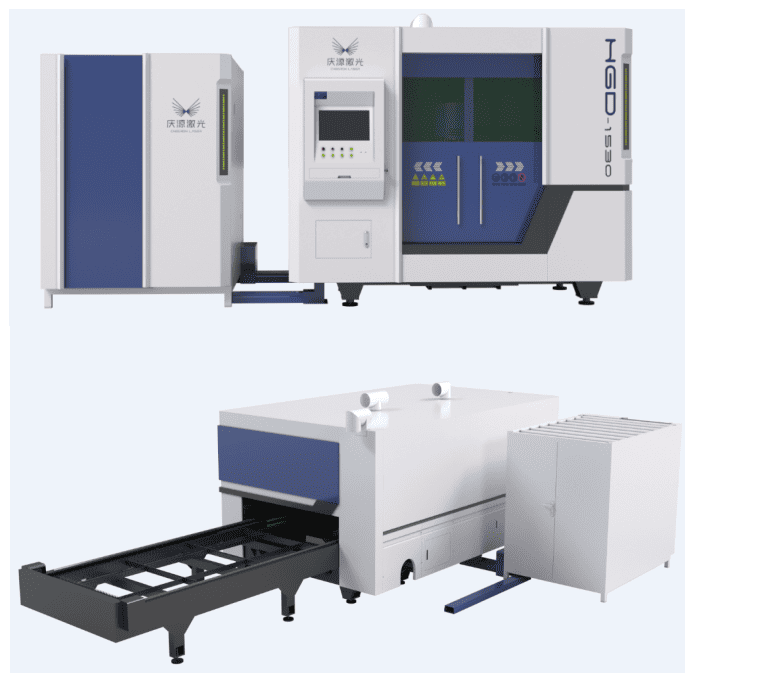
Laser cutting technology has proven to be exceptionally precise, particularly when working with aluminum materials. The process involves the use of a highly focused laser beam to cut through the material, allowing for intricate designs and achieving tight tolerances. The precision of laser cutting in aluminum is influenced by several factors:
Focused Laser Beam: The fundamental aspect contributing to the precision of laser cutting is the focused laser beam itself. The beam is directed with pinpoint accuracy onto the aluminum surface, allowing for meticulous cutting and shaping.
Minimal Heat Affected Zone (HAZ): Laser cutting generates minimal heat, resulting in a limited Heat Affected Zone (HAZ) in the surrounding material. This characteristic is crucial when working with aluminum, as it helps prevent distortion and ensures the retention of the material’s structural integrity.
Computer Numerical Control (CNC) Technology: Laser cutting machines are often equipped with Computer Numerical Control (CNC) technology, enabling precise control over the cutting process. CNC systems use digital instructions to guide the laser accurately, ensuring consistency and repeatability in the cuts.
Material Compatibility: Aluminum is particularly well-suited for laser cutting due to its reflective properties. The material efficiently absorbs the laser energy, facilitating a clean and precise cut without excessive scattering of the beam.
High Speed and Efficiency: Laser cutting operates at high speeds, allowing for efficient and rapid processing of aluminum sheets. The combination of speed and precision makes laser cutting an ideal choice for industries where time-sensitive and accurate production is paramount.
Versatility in Thickness: Laser cutting can handle a wide range of aluminum thicknesses, providing versatility in manufacturing applications. Whether it’s thin aluminum sheets or thicker sections, the technology can adapt to various material dimensions while maintaining precision.
Reduced Tool Wear: Unlike traditional cutting methods that involve physical tools, laser cutting does not suffer from tool wear. This absence of wear ensures consistent precision over time, reducing the need for frequent tool replacements and maintenance.
In conclusion, the precision of laser cutting in aluminum materials is unparalleled, making it a favored technology in industries that demand intricate designs, tight tolerances, and reliable efficiency, such as aerospace and electronics. The combination of a focused laser beam, minimal heat impact, CNC technology, material compatibility, high speed, versatility in thickness, and reduced tool wear collectively contribute to the exceptional precision achieved through laser cutting processes.
What Types of Lasers Are Commonly Used for Cutting Aluminum?
In the machine industry, the utilization of lasers for cutting aluminum has become a prominent method, and among the various types of lasers available, fiber lasers stand out as a common and effective choice. Fiber lasers operate by generating a laser beam through optical fibers, showcasing exceptional power and efficiency in their performance. Several factors contribute to the popularity of fiber lasers in the context of cutting aluminum:
Optical Fiber Technology:
Fiber lasers leverage optical fibers to guide and amplify the laser beam. This technology enables the efficient delivery of high-powered laser energy to the cutting surface.
The optical fiber system allows for a more flexible and compact design, making fiber lasers suitable for integration into various cutting machines.
High Power and Precision:
Fiber lasers are capable of delivering high levels of power, facilitating rapid and efficient aluminum cutting processes. This is particularly advantageous in industrial settings where productivity is a key consideration.
The precision of fiber lasers ensures that intricate patterns and fine details can be achieved during the cutting process, meeting the demands of diverse applications.
Reflective Properties of Aluminum:
Aluminum is known for its reflective properties, posing challenges for some traditional laser systems. However, fiber lasers are well-suited to handle reflective materials.
The wavelength of the laser beam in fiber lasers is effectively absorbed by aluminum, preventing issues related to reflections that might occur with other types of lasers.
Consistency in Cutting Results:
Fiber lasers provide consistent cutting results, ensuring uniformity across the entire aluminum surface. This reliability is crucial in manufacturing processes where product quality and dimensional accuracy are paramount.
Reduced Maintenance Requirements:
Fiber lasers often have a lower maintenance burden compared to other types of lasers. The absence of intricate optical components and the durability of optical fibers contribute to a more robust and reliable cutting system.
Energy Efficiency:
Fiber lasers are known for their energy efficiency, converting a higher percentage of electrical input into laser output. This not only reduces operational costs but also aligns with the growing emphasis on sustainability in industrial practices.
Versatility in Thickness:
Fiber lasers exhibit versatility in cutting aluminum of various thicknesses. This adaptability makes them suitable for a wide range of applications, from thin sheets to thicker plates.
How Does the Speed of Laser Cutting for Aluminum Compare to Other Cutting Methods?
Laser cutting stands out in the machine industry due to its unparalleled speed and efficiency, particularly when compared to conventional cutting methods such as sawing or milling. Several factors contribute to the remarkable speed of laser cutting, making it a preferred choice for various industrial applications:
Non-Contact Nature: One of the key advantages of laser cutting is its non-contact nature. Unlike traditional methods that involve physical contact between the cutting tool and the material, laser cutting employs a focused beam of light to melt, burn, or vaporize the material without any direct touch. This non-contact approach reduces friction and wear on the cutting tool, resulting in faster cutting speeds.
Precision and Accuracy: Laser cutting systems are renowned for their high precision and accuracy. The focused laser beam allows for intricate and detailed cuts with minimal material wastage. The ability to follow precise computer-aided designs (CAD) ensures that the cutting process is optimized for speed without compromising accuracy.
Versatility in Material Thickness: Laser cutting excels in handling a wide range of material thicknesses. Whether it’s thin sheets or thicker plates, laser cutting machines can adapt to different material requirements, ensuring consistent speed across various applications. This versatility is a significant advantage over some traditional methods that may struggle with diverse material thicknesses.
Automation Integration: Laser cutting systems are often integrated with advanced automation technologies, further enhancing their speed. Automated loading and unloading of materials, along with real-time adjustments based on sensor feedback, contribute to continuous and uninterrupted cutting processes. This level of automation minimizes downtime and significantly improves overall efficiency.
Reduced Setup Times: Setting up a laser cutting machine for a new job is typically quicker compared to traditional methods. With the ability to change cutting parameters rapidly through computerized controls, laser cutting machines can transition from one job to another swiftly. This agility is crucial for industries with frequent product changes or customizations.
Minimal Material Distortion: Laser cutting produces minimal heat-affected zones, reducing the likelihood of material distortion. Traditional methods, such as sawing or milling, often generate more heat during the cutting process, leading to thermal distortion. The controlled and focused energy of lasers minimizes this effect, contributing to consistent speed and quality.
Are There Specific Design Considerations for Optimizing Laser Cutting of Aluminum?
Specific design considerations play a pivotal role in optimizing the overall efficiency and quality of the production. These considerations are crucial for ensuring that the laser cutting process not only meets but exceeds the desired outcomes. Here are key design considerations:
Hole Size:
Precision Requirements: Laser cutting is renowned for its ability to achieve small and precise holes in materials. Consider the specific precision requirements of the project and leverage the capabilities of laser technology to produce holes with minimal deviation from the intended size.
Tolerance Limits: Understand the tolerance limits associated with the laser cutting equipment being used. This knowledge helps in designing holes that fall within the acceptable range of deviation.
Inner Geometries:
Efficient Material Removal: When designing components, consider incorporating inner geometries that facilitate efficient material removal during the laser cutting process. This not only enhances the speed of production but also reduces waste and ensures that the final product adheres to design specifications.
Complex Shapes: Laser cutting allows for the creation of intricate and complex shapes. Capitalize on this capability by designing inner geometries that might be challenging or impractical with traditional cutting methods.
Cutting Paths:
Optimized Efficiency: The design of cutting paths has a direct impact on the overall efficiency of the laser cutting process. By strategically planning and optimizing cutting paths, manufacturers can minimize unnecessary movements of the laser head, thereby reducing production time and resource utilization.
Reduced Heat Affected Zone (HAZ): Thoughtful consideration of cutting paths can also help in minimizing the heat affected zone (HAZ) – the area around the cut where the material experiences thermal changes. This is particularly important when working with aluminum, as excessive heat can affect the material’s properties.
What Safety Precautions Should Be Taken When Using Laser Cutting for Aluminum?
Ensuring safety when using laser cutting for aluminum is paramount, as this process involves the use of high-powered lasers that can pose various hazards. Implementing a comprehensive set of safety precautions is essential to protect operators and maintain a secure working environment.
Protective Gear:
Safety Glasses: Laser cutting emits intense light that can be harmful to the eyes. Operators must wear safety glasses with appropriate filtering to shield their eyes from the laser beam.
Gloves: Given the potential for sharp edges on aluminum and the risk of burns, operators should wear heat-resistant gloves to protect their hands during the handling of materials.
Ventilation:
Fume Extraction System: Laser cutting aluminum produces fumes and particles that can be hazardous when inhaled. Employing a reliable fume extraction system is crucial to remove these by-products and maintain air quality within the workspace.
Well-Ventilated Area: Conduct laser cutting in a well-ventilated space to ensure that any residual fumes are effectively dispersed. Adequate airflow reduces the risk of operators inhaling harmful substances.
Machine Maintenance:
Regular Inspections: Conduct routine inspections of the laser cutting machine to identify and address any potential issues promptly. This includes checking the condition of the laser source, optics, and other critical components to ensure they are functioning correctly.
Alignment Checks: Proper alignment of the laser beam is essential for precision cutting and, more importantly, for safety. Regularly check and align the optics to maintain the accuracy of the cutting process.
Emergency Stop Procedures: Ensure that all operators are trained in emergency stop procedures and that these are clearly marked and easily accessible. In the event of any unforeseen circumstances, quick response capabilities are crucial to prevent accidents.
Training and Education:
Operator Training: Provide comprehensive training to operators on the safe use of laser cutting equipment, including emergency protocols, proper material handling, and the correct use of protective gear.
Safety Guidelines:
Clearly communicate and display safety guidelines in the workspace, emphasizing the importance of adherence to protocols and the consequences of neglecting safety measures.
Fire Prevention
Material Compatibility:
Ensure that the laser cutting machine is set up to handle aluminum safely. Different materials may have specific requirements, and adjustments may be needed to prevent overheating or ignition during the cutting process.
Fire Suppression Equipment:
Have appropriate fire suppression equipment, such as fire extinguishers, readily available in the vicinity of the laser cutting machine. Regularly check and maintain this equipment to ensure its effectiveness in case of emergencies.
Implementing and strictly adhering to these safety precautions will not only protect individuals operating the laser cutting equipment but also contribute to the overall efficiency and longevity of the machinery. Regular training, maintenance, and a culture of safety awareness are crucial elements in creating a secure working environment in the machine industry.
Can Intricate or Complex Designs Be Achieved With Laser Cutting on Aluminum?
Laser cutting technology has revolutionized the manufacturing landscape, particularly in the realm of aluminum fabrication, enabling the creation of intricate and complex designs with unparalleled precision. This advanced technique utilizes a focused laser beam to cut through materials with exceptional accuracy, making it an ideal choice for a wide range of applications in the machine industry. Here’s a detailed exploration of how intricate and complex designs can be achieved with laser cutting on aluminum:
Precision and Accuracy: Laser cutting is renowned for its ability to provide high levels of precision and accuracy. The focused laser beam can achieve fine details, ensuring that intricate patterns and complex designs are reproduced with consistency and reliability.
Versatility of Materials: Laser cutting is not limited to a specific type of material, making it versatile for various applications. When it comes to aluminum, the process is particularly effective due to the material’s suitability for laser cutting. The technology can handle a broad range of aluminum alloys, allowing for the creation of intricate designs on different grades of the metal.
Minimal Material Waste: Traditional cutting methods often result in significant material waste, but laser cutting minimizes this issue. The focused laser beam enables precise cuts, reducing the amount of material that goes to waste. This efficiency is especially valuable when working with expensive materials like aluminum.
Complex Geometries and Shapes: Laser cutting is capable of handling complex geometries and intricate shapes that might be challenging or impossible to achieve with traditional cutting methods. This is crucial in the machine industry, where intricate components and specialized parts are often required for sophisticated machinery.
Intricate Patterns and Textures: Beyond merely cutting through the material, laser cutting can be used to create intricate patterns and textures on the surface of aluminum. This capability opens up new possibilities for designers, allowing them to incorporate visually appealing and functional elements into their projects.
Fine Detailing for Electronic Components: In the realm of electronic devices, where miniaturization and precision are paramount, laser cutting on aluminum is indispensable. The technology can be employed to produce intricate components with fine detailing, contributing to the overall efficiency and functionality of electronic devices.
Customization and Prototyping: Laser cutting is highly conducive to customization, enabling manufacturers to produce unique and tailored designs. It is also an excellent tool for prototyping, allowing engineers and designers to quickly iterate and refine their concepts before mass production.
What Factors Influence the Cost of Laser Cutting for Aluminum?
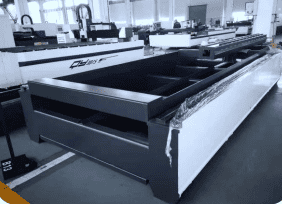
The cost of laser cutting for aluminum is influenced by various factors that play a crucial role in determining the overall expenses associated with this precision machining process. To delve deeper into the key factors influencing costs, consider the following bullet points:
Material Thickness.
Energy Consumption:
Thicker aluminum sheets absorb more energy, requiring higher laser power to achieve a clean and precise cut.
Processing Time.
Thicker materials take longer to cut as the laser must penetrate through more substance, contributing to increased labor costs.
Complexity of Design.
Precision Requirements:
Complex designs with intricate details necessitate a higher level of precision during laser cutting, demanding skilled operators and specialized equipment.
Programming and Set-Up:
Elaborate designs may require more time for programming the laser cutting machine and setting up the parameters correctly.
Volume of Production.
Economies of Scale:
High-volume production can lead to economies of scale, where the fixed costs associated with machine setup and programming are distributed across a larger number of units, reducing the cost per unit.
Efficiency Gains:
Laser cutting efficiency tends to increase with volume, as the continuous operation of the machine for a larger production run minimizes downtime associated with loading and unloading materials.
How Environmentally Friendly Is Laser Cutting for Aluminum Compared to Other Methods?
Laser cutting for aluminum stands out as an environmentally friendly option in the manufacturing industry when compared to certain traditional methods. The following points elaborate on the eco-friendly aspects of laser cutting for aluminum:
Material Efficiency:
Laser cutting is highly precise, allowing for optimal material usage with minimal waste. The focused laser beam accurately cuts through aluminum sheets, ensuring that the material is utilized efficiently without unnecessary loss.
The precision of laser cutting also enables nesting, a technique where multiple parts are arranged closely together on a single sheet to minimize scrap material. This reduces the overall material consumption, making it a sustainable choice.
Minimal Waste Production:
Traditional cutting methods, such as mechanical cutting or abrasive methods, often result in significant material wastage due to the wider cutting kerf and imprecise cutting lines. In contrast, laser cutting produces minimal waste, contributing to a more sustainable manufacturing process.
The reduced waste not only saves on raw materials but also decreases the environmental impact associated with disposal and the need for additional resources to produce new materials.
Energy Efficiency:
Laser cutting systems are designed to be energy-efficient. The use of focused laser beams requires less power compared to some traditional cutting methods, such as plasma or water jet cutting. This results in lower energy consumption during the manufacturing process, aligning with the global push for energy conservation and sustainability.
Additionally, advancements in laser technology continue to improve efficiency, making laser cutting an increasingly attractive option from an environmental perspective.
Reduced Emissions:
Unlike certain traditional methods that may involve the use of chemicals or emit harmful fumes, laser cutting typically produces fewer emissions. The absence of physical contact between the cutting tool and the material reduces the generation of harmful byproducts, contributing to cleaner air quality in the manufacturing environment.
Versatility and Adaptability:
Laser cutting is versatile and adaptable to various designs and thicknesses of aluminum, allowing for the production of intricate and complex shapes with high precision. This versatility reduces the need for secondary processes and treatments, further minimizing the environmental impact associated with additional manufacturing steps.
Conclusion
In conclusion, laser cutting for aluminum emerges as a pivotal technology in the contemporary landscape of metal fabrication, showcasing unparalleled precision, efficiency, and versatility. As we navigate the conclusion of this educational guide, it becomes evident that laser cutting plays a central role in shaping the future of aluminum processing across diverse industries. From its crucial applications in aerospace, where intricate designs and lightweight structures are imperative, to its indispensable role in crafting precision electronic components, the impact of laser cutting reverberates across various sectors.
This technology has proven itself as a transformative force, allowing for intricate designs and intricate cuts that were once thought impossible or too labor-intensive. Professionals in the metal fabrication industry, as well as curious enthusiasts, stand to benefit significantly from a deep understanding of laser cutting’s advantages, considerations, and safety measures. Recognizing the significance of this technology not only broadens one’s knowledge base but also ensures optimal results in the dynamic and evolving realm of metal fabrication. Whether you are embarking on the exploration of laser cutting possibilities or seeking to enhance your current processes, this comprehensive guide serves as a valuable resource, offering insights and practical knowledge into the intricate world of laser cutting for aluminum.